在石油钻井过程中,钻具在地层内沿着预定的方向螺旋前进,外壁与井壁或者套管接触,产生持续而强大的摩擦力,而钻具接头一般要比管体的外径大20%~30%,所以钻具接头外壁是整个钻具最易磨损的部位,而目前最为常见的保护措施就是在接头表面堆焊耐磨带材料。当前,钻具接头堆焊耐磨带技术比较成熟,国内使用的耐磨带焊丝类型较多,耐磨性亦有所差异。
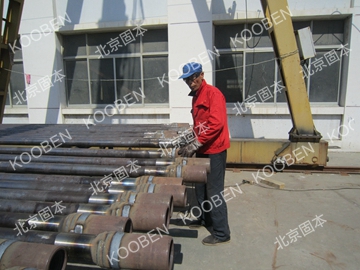
为了延长钻杆等钻具的使用寿命,或对缺陷耐磨带进行修复,亦或是在原有耐磨带层或在去除层上再次堆焊耐磨带,即“二次堆焊”。主要介绍一下目前比较常用的耐磨带——KB100耐磨带焊丝的二次堆焊技术。文中主要介绍一下耐磨带二次堆焊技术。
1 二次堆焊技术简介
现在结合二次堆焊工艺流程图和公司生产实际,简要介绍一下KB100耐磨带焊丝的二次堆焊技术。二次堆焊时,要注意以下两点:
(1)焊前必须清理堆焊区域的水、油污、锈斑等脏物,必须确保无裂纹、气孔等缺陷,否则,二次堆焊完成后,裂纹缺陷会纵向延伸,不但延伸至新堆焊耐磨带上,而且有可能延伸至钻具接头基材内,而当钻具在地层钻进时,轻则造成焊带脱落,严重时会造成钻具断裂。
(2)二次堆焊前的底层区域,无论是基材还是同型号耐磨带,对二次焊带的融合、成型、附着力等因素影响不明显。结合公司生产实际,介绍一下KB100耐磨带焊丝的二次堆焊技术。某用户的一批加重钻杆,接头上原有KB100耐磨带,该耐磨带存在一些缺陷,用户要求在其原有耐磨带位置上堆焊同型耐磨带。经检验,原有KB100耐磨带区域存在气孔、裂纹等缺陷,必须对原有耐磨带进行部分或全部清除,直到消除这些缺陷才能进行二次堆焊。可以用肉眼清晰地看到的表面裂纹。首要工作就是要去除缺陷层。
1.1 去除带有缺陷的耐磨带
无论耐磨带区域还是钻杆基材,都不允许出现气孔、起皮或裂纹等缺陷。原有缺陷耐磨带缺陷层较厚,为了去除硬度较大的缺陷层,可用碳弧气刨进行预处理,碳弧气刨处理后,表面粗糙不平,附着许多焊渣,还要对其表面进行轻度打磨。如果原有的耐磨带已经完全去除,缺陷延伸到钻杆基材内,那么还要对基材进行深入去除,直到基材上没有缺陷为止。对于钻杆基材来说,除非用户另行要求,车削深度一般不超过9 mm,否则影响钻具接头的强度。
1.2对去除区域的检测
对车削后的区域及其两侧26 mm宽的热影响区进行探伤检测,如果表面有裂纹,则需要继续深入去除,直到探伤无裂纹为止。
1.3补焊填充
如果缺陷层未延伸至基材,则只需去除带有缺陷的耐磨带层,在其上堆焊新耐磨带即可;如果缺陷层延伸至基材,继续去除基材缺陷层后,还需要用低碳钢对钻杆损失的基材进行补焊填充,与接头表面齐平。填充后,对填充区域其两侧26 mm宽的区域进行探伤检测,如果发现表面有裂纹,需要车削掉填充材料重新堆焊,直到无缺陷为止。采用低碳钢补焊填充后,表面仍然出现气孔缺陷,这就需要重新车削、补焊低碳钢,直到没有缺陷为止。
1.4二次堆焊KB100耐磨带
焊前需要对堆焊区域进行预处理,清理表面的水、油污和锈斑等脏物,再对堆焊区域进行预热,按照工艺要求设置焊接参数,对钻杆接头进行二次堆焊耐磨带,焊接过程和参数与第一次焊接时的相应参数相同。焊接完成后,对焊渣进行简单清理,并及时包覆保温套,对焊带进行保温,使其缓慢冷却,这样可防止高温焊带急速降温产生应力,出现裂纹缺陷。
1.5 焊后检验
对耐磨带的检验包括外观检验和无损检测。外观检验包括检验焊缝的外形轮廓,测量焊缝的尺寸(包括焊缝宽度、高度),还要观察有无气孔、起皮或裂纹等缺陷,外形轮廓检验。磁粉检测包括对焊缝及其两侧26 mm宽的母材热影响区进行检测,检验是否有裂纹存在。检验合格后,二次堆焊最终完成。
2结论
按照去除缺陷层并检测缺陷层、补焊填充、二次堆焊、焊后检验等工艺流程,已经多次完成了KB100耐磨带焊丝的二次堆焊技术服务,收到满意的焊接效果,得到用户的一致认可。